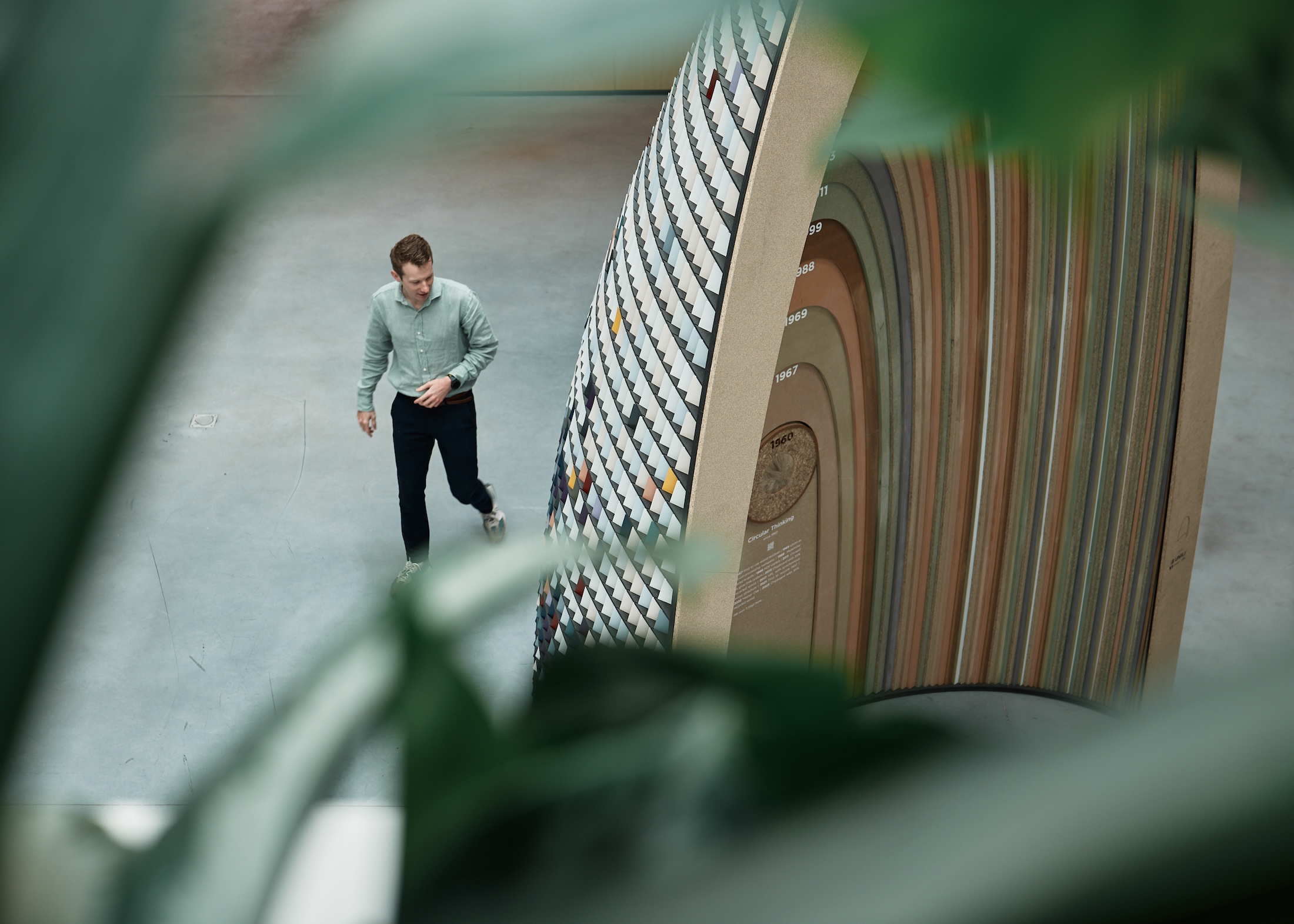
the Fingerprint
SCOPE
Unilin, Belgium’s largest wood recycling company and a global leader in interior design and construction solutions, asked ncbham to design a sculptural display reflecting their core values such as sustainable design and environmental commitment.
Through an innovative co-creative process, we developed a versatile and flexible design, optimizing material and resource use. The result is an impressive, vibrant, double-skinned piece that “moves” with the viewer’s eye. It not only serves its display purpose but also symbolizes Unilin’s dedication to the environment, using only the company’s recycled panels.
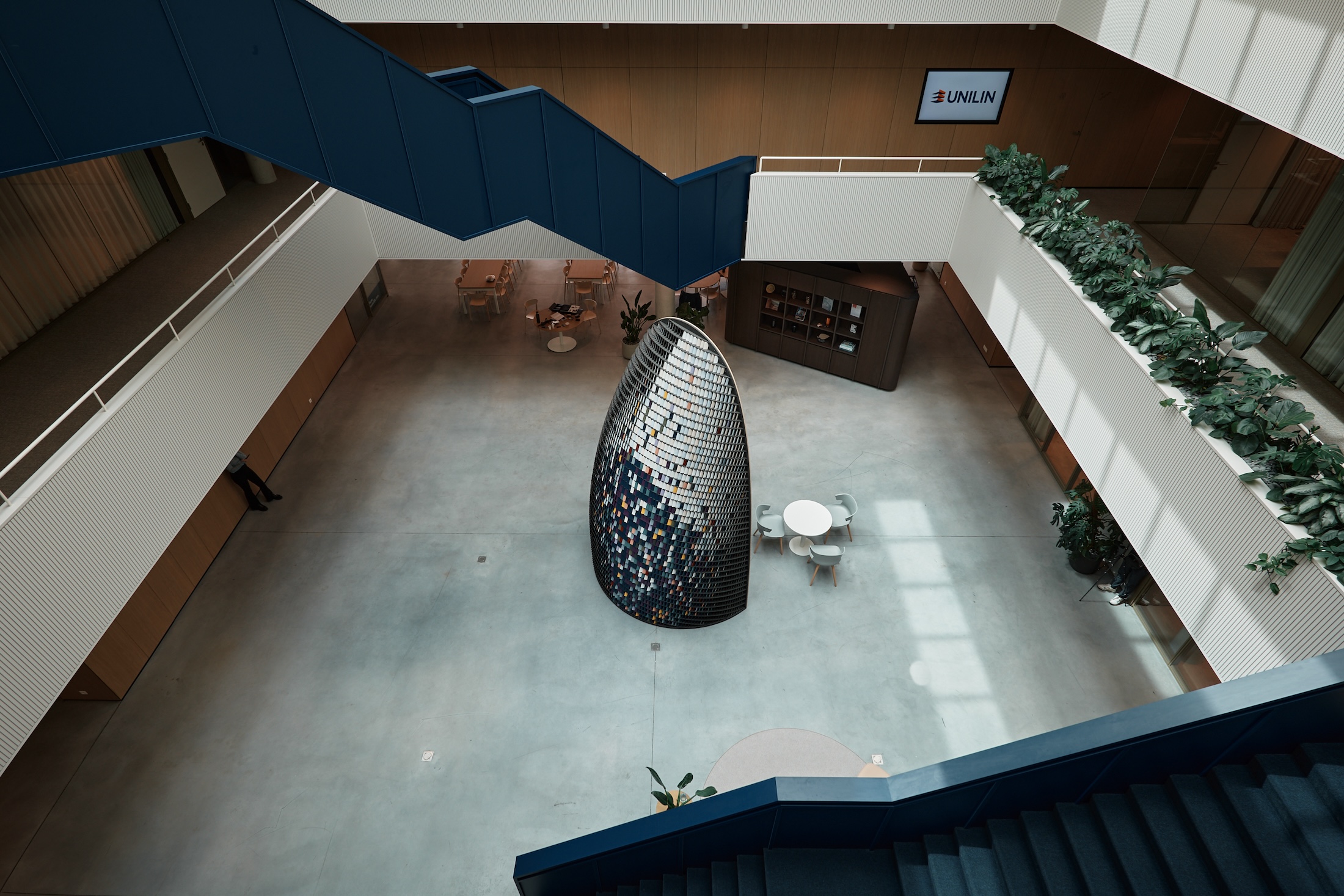
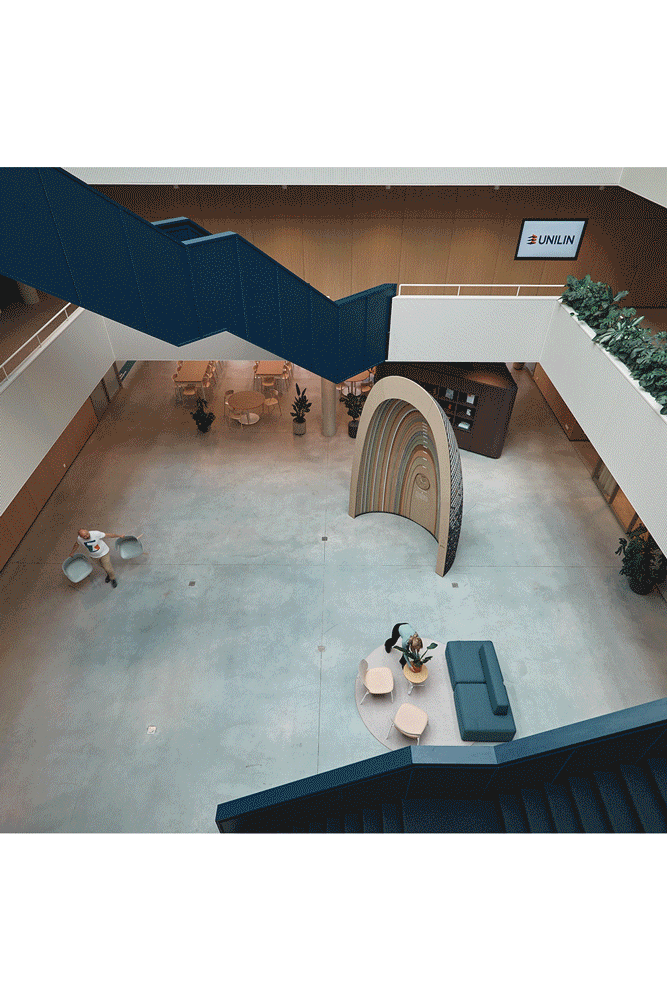
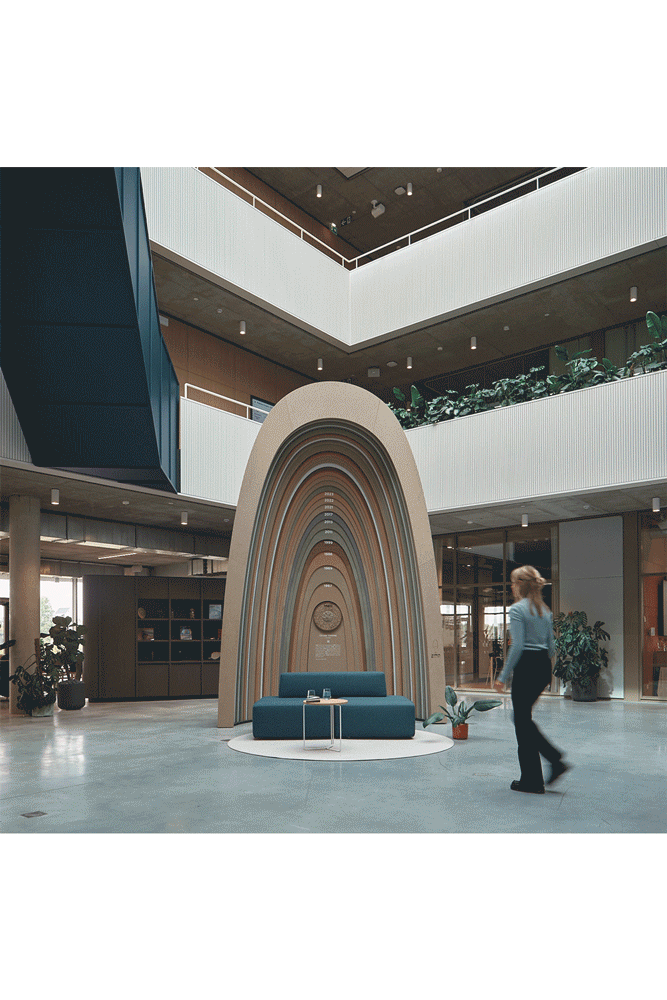
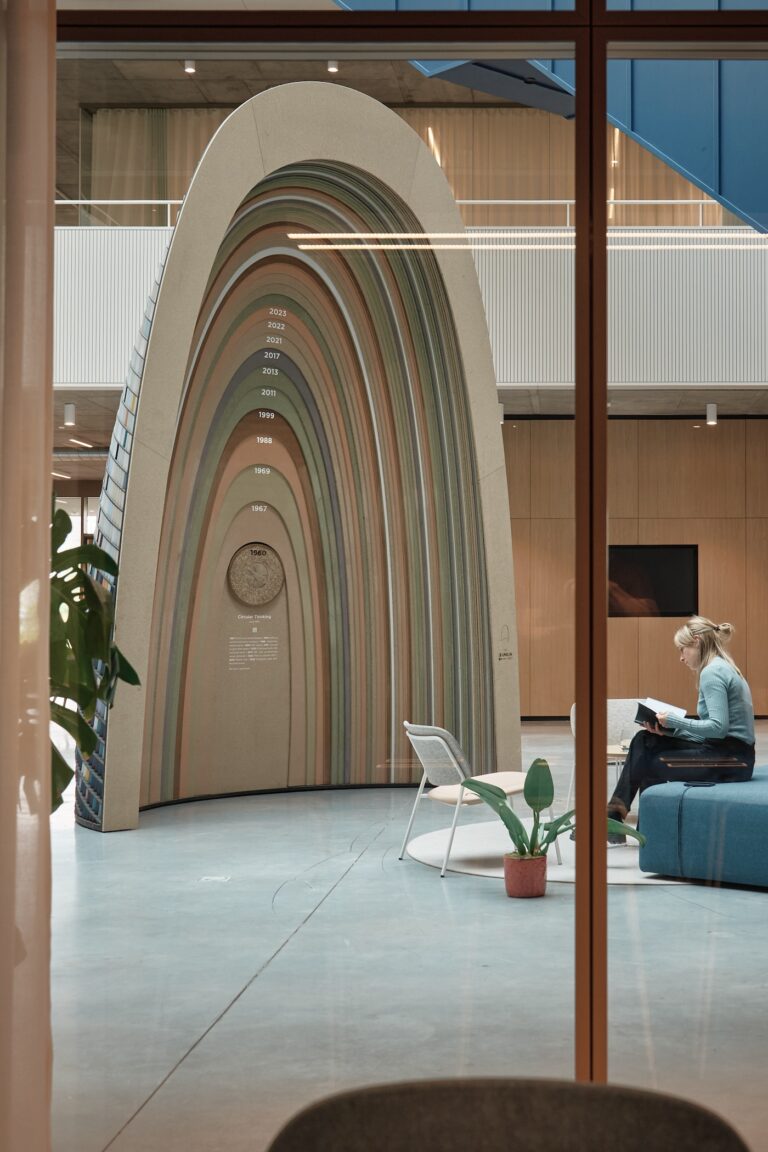

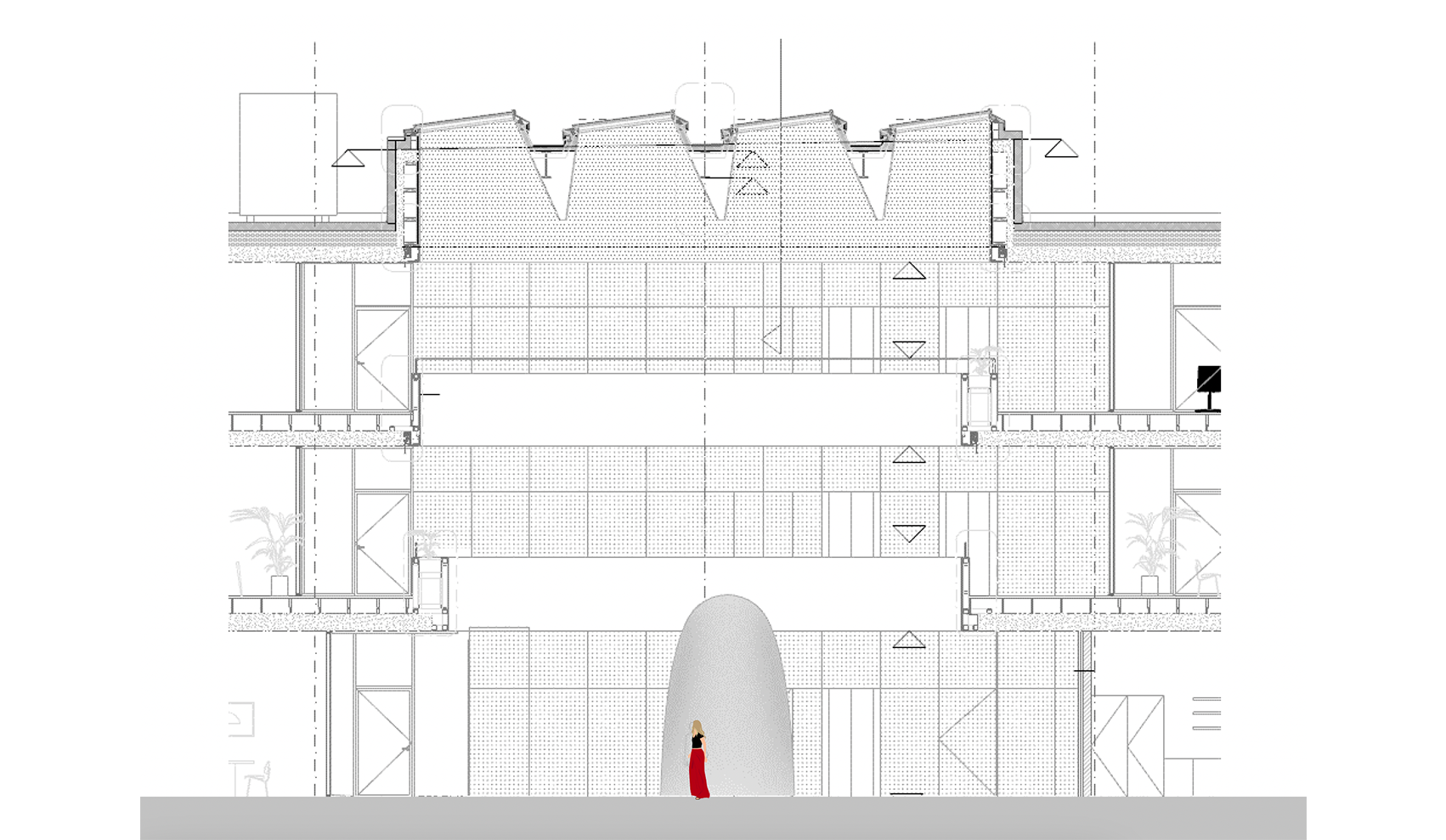
DESIGN APPROACH
The client’s request was for an artistic, versatile piece that would creatively highlight the product’s potential and present the company’s story while fitting a limited budget. The piece would be placed in the center of the atrium of their new headquarters, allowing for flexible use of the space for events.
Our design addressed the challenge of reimagining product display by combining modularity, minimalism, spatial innovation, and interactive storytelling. This approach ensured that the sculpture was not only visually striking but also functional, educational and adaptable to different uses within the atrium. We developed a double-sided structure with “inner” and “outer” faces, using exclusively Unilin products, highlighting both the utilitarian and aesthetic qualities of the panels.
The inner face features the core range of Unilin panels, usually hidden within structures and not typically considered aesthetically pleasing. These ‘nude’ panels represent Unilin’s roots and foundational elements, displayed in their raw form to reflect the brand’s simplicity and authenticity. The outer face showcases the vibrant range of ready-made Unilin color samples, creating a dynamic, colorful skin that allows for easy updates with new finishes. The proposed gradient is inspired by the architecture, transitioning from the stair’s dark blue to the atrium’s sky white balconies with complementary oranges, and analogous purples. The diverse white finishes create a subtle interplay of matte and glossy textures, warm and cool tones.
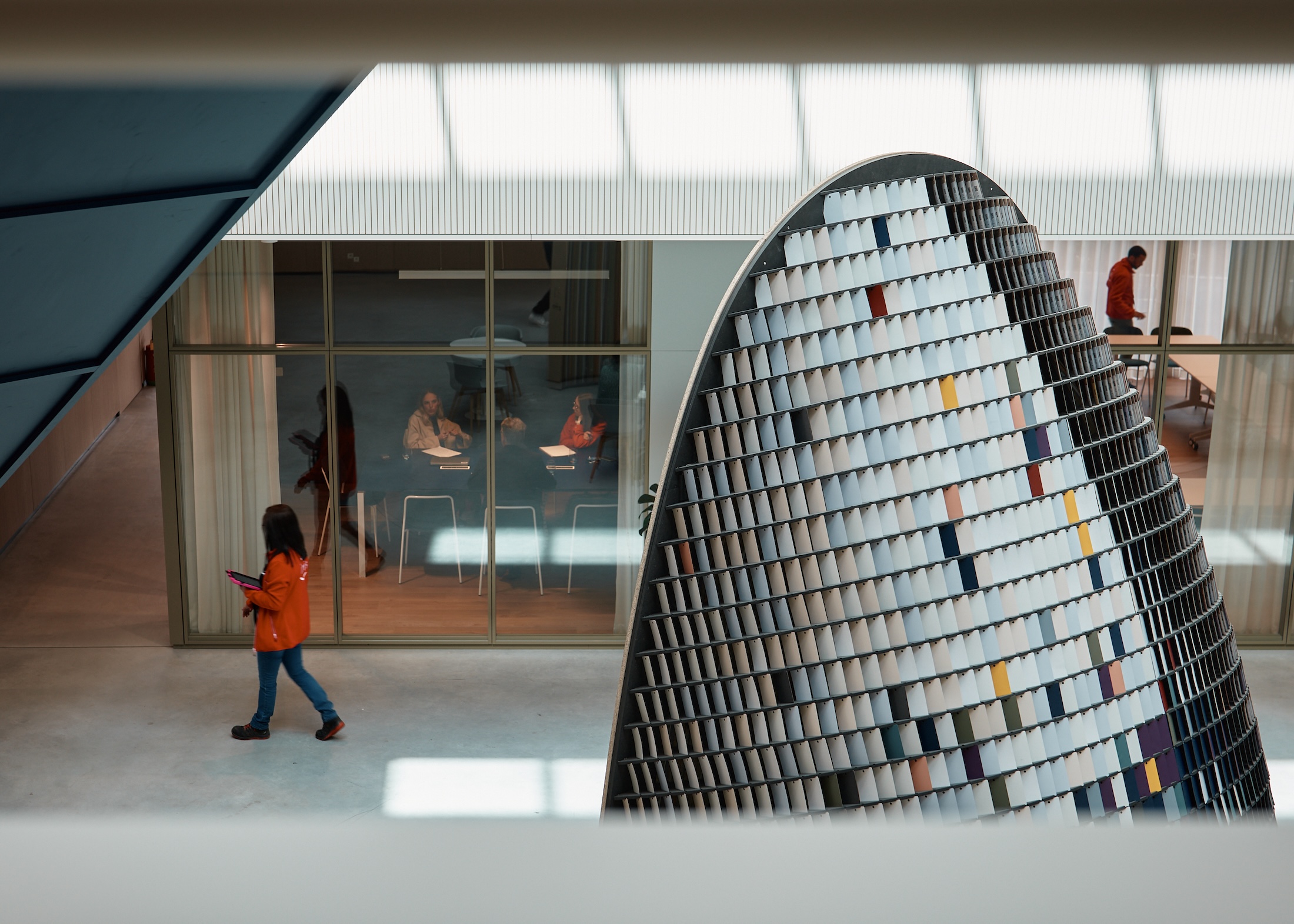
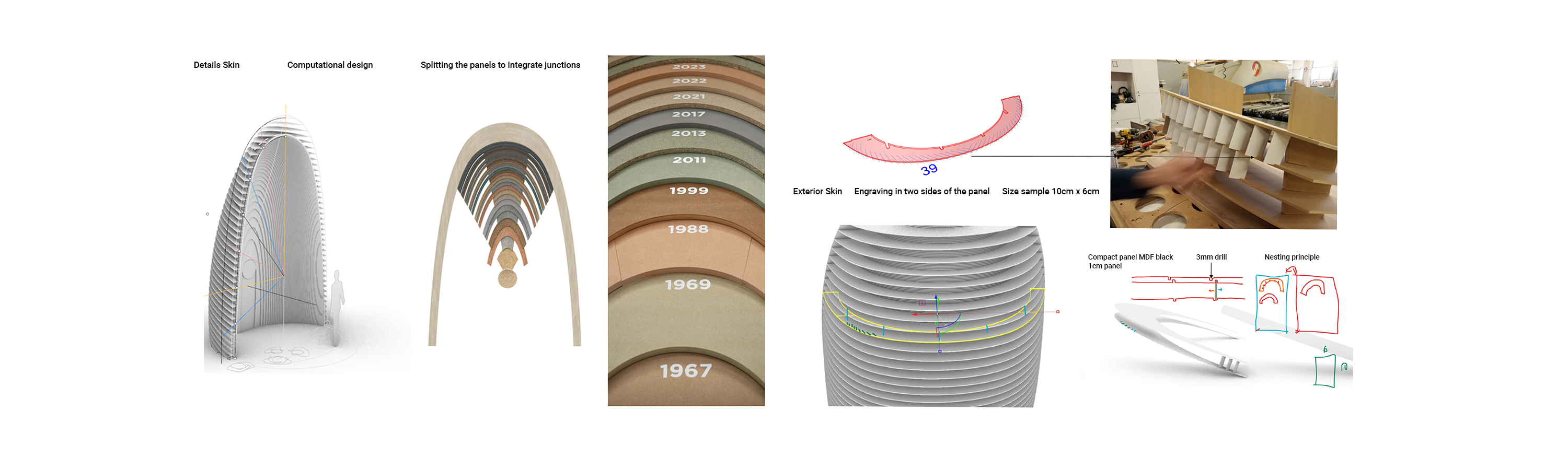
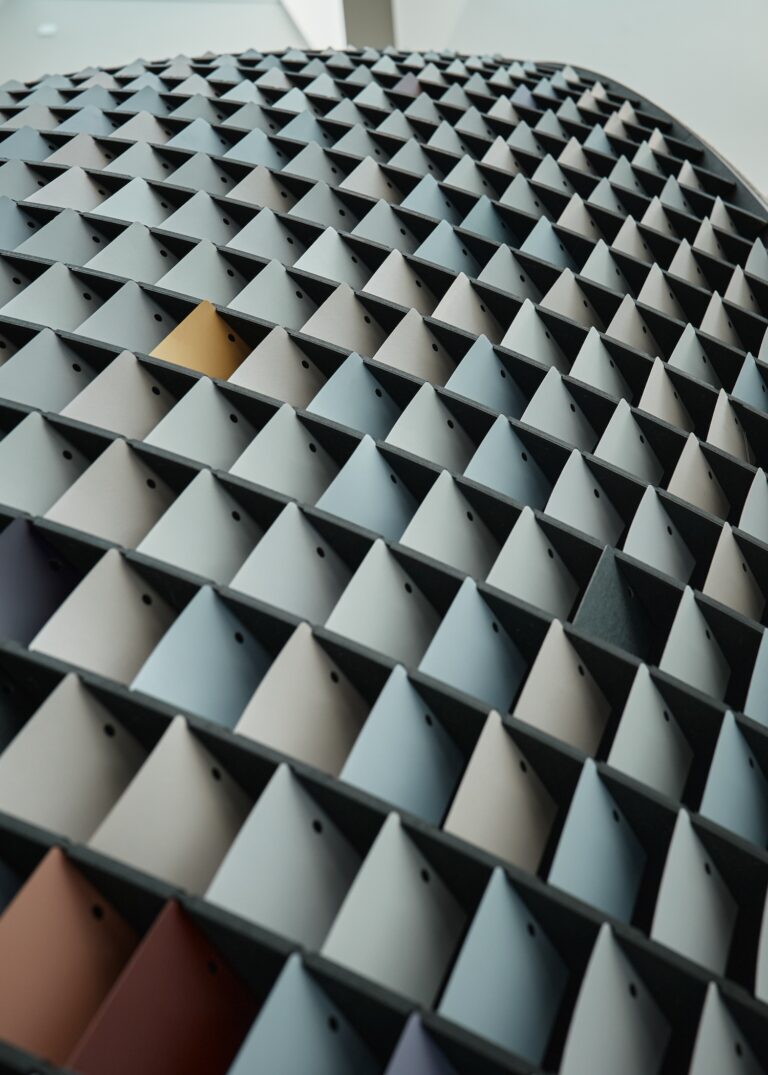
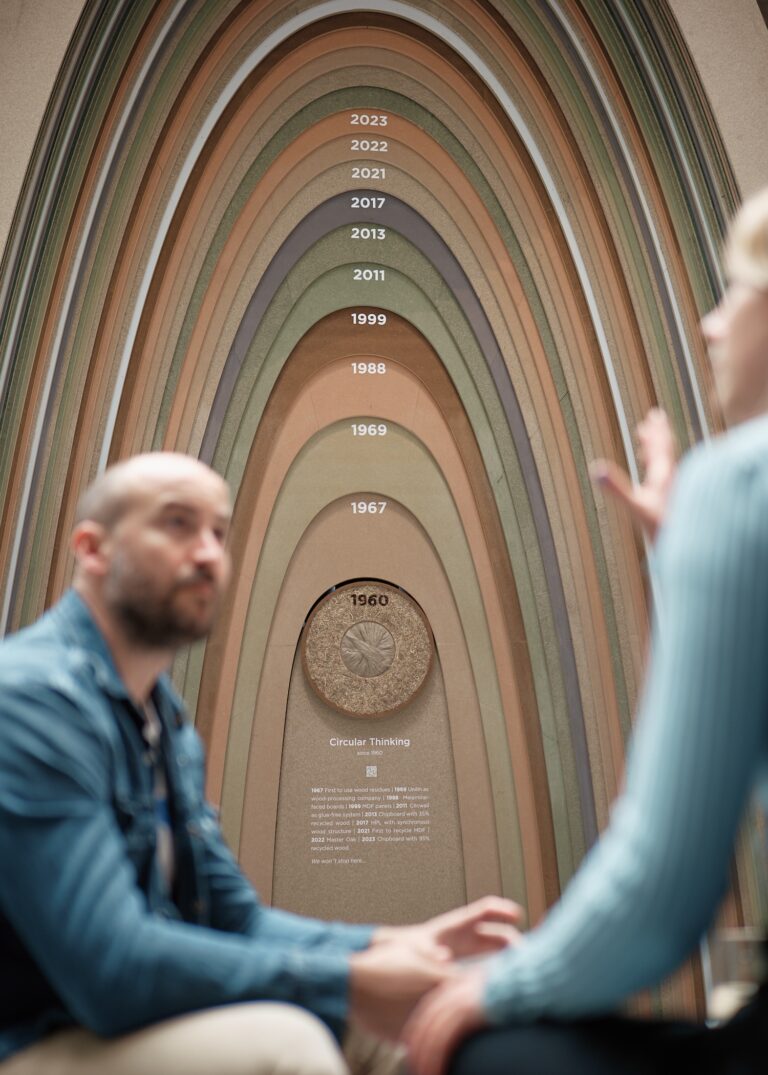
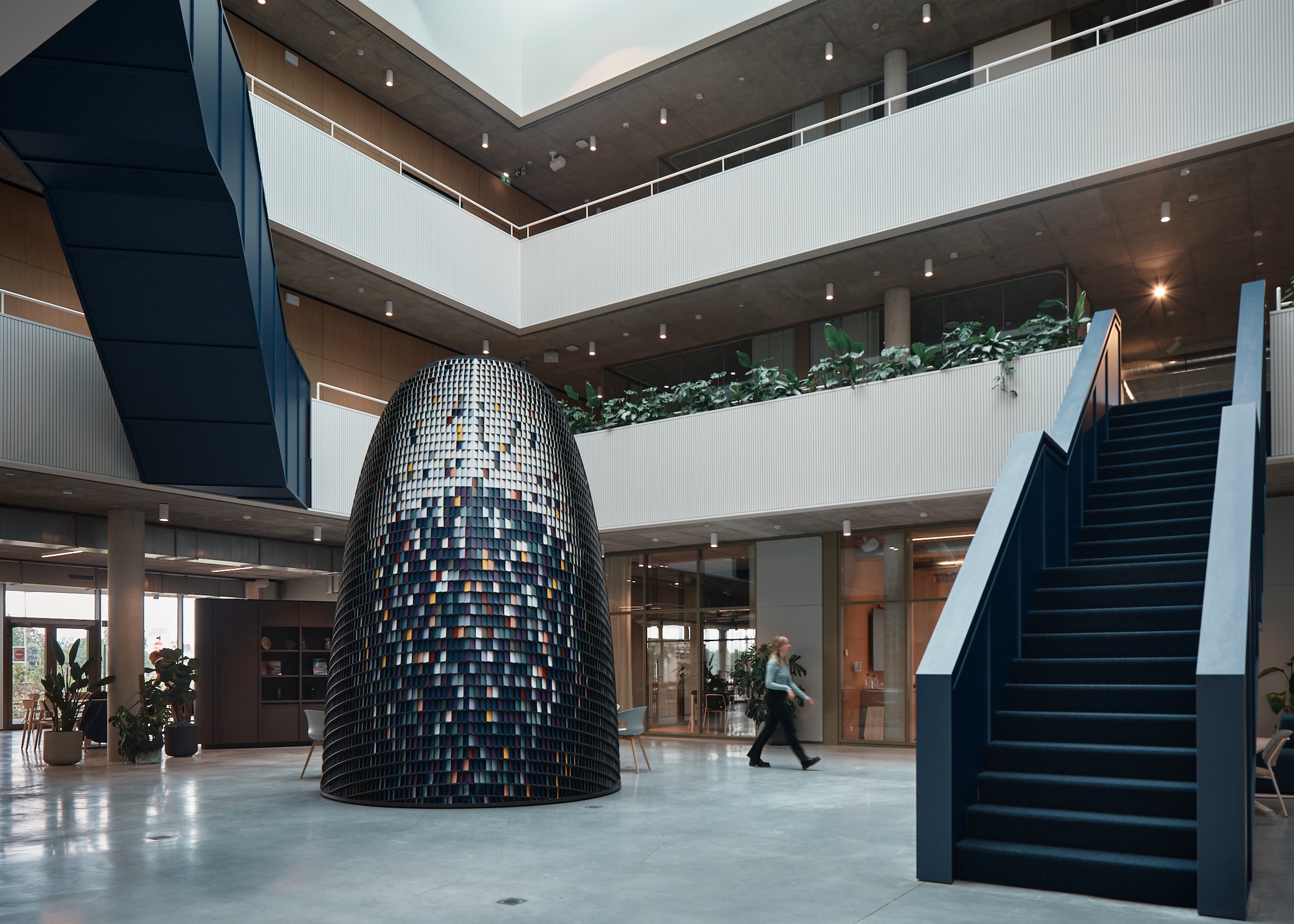
Symbol of sustainability
The piece is designed to be modular and have a minimal footprint, ensuring easy mobility to free up space for events. Its hollow structure maintains a strong presence in the atrium while occupying minimal floor space. This design choice as well as the final shape and structure of the piece was the result of computational design programming that permitted fast and precise testing, helping us to ensure functionality without compromising on aesthetics or practicality.
The sculpture also served as a spatial divider, creating a cocoon-like area within the larger atrium. This “room within a room” concept provided a semi-enclosed space for visitors to engage with the display more intimately, enhancing their experience and interaction with the product.
Finally, the piece was designed to be a playful and engaging medium for telling the story of Unilin. It detailed the brand’s timeline, highlighting significant milestones and ecological decisions, illustrating Unilin’s long-term environmental commitment and innovation. By using only Unilin recycled panels for the piece, we ensured that the primary components of our design contribute to waste reduction, making out of the sculpture not only an artistic and functional piece, but also a model of responsible and conscientious design, thus echoing fully Unilin’s core values.
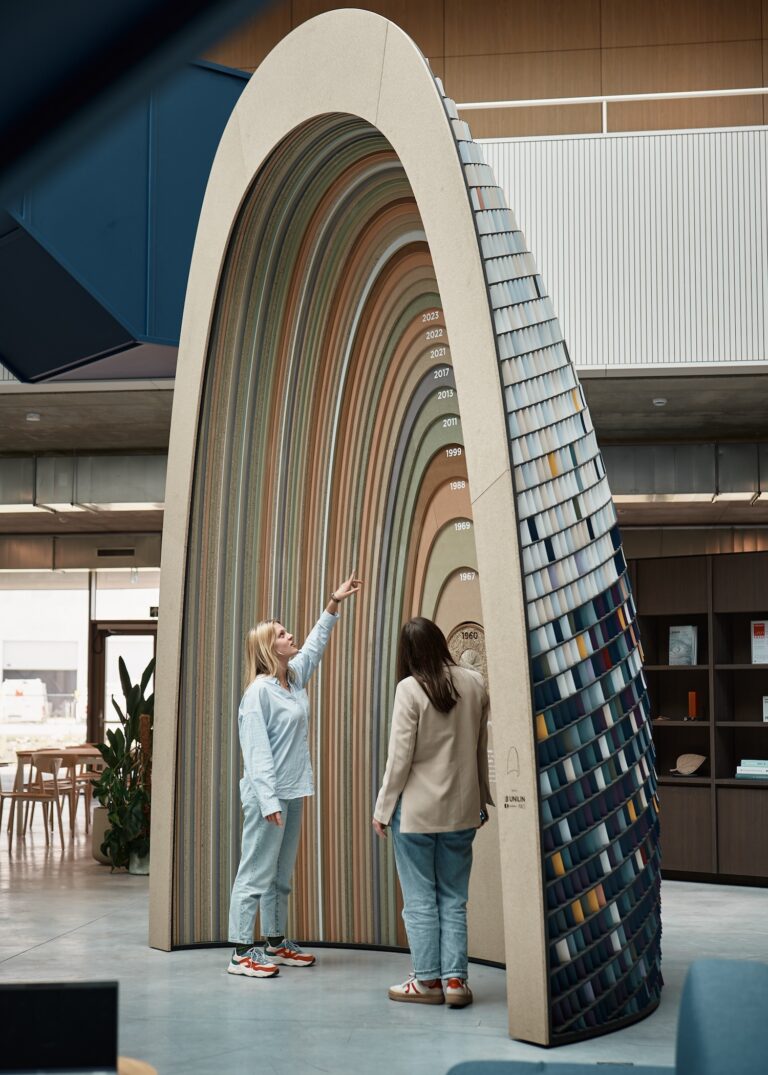
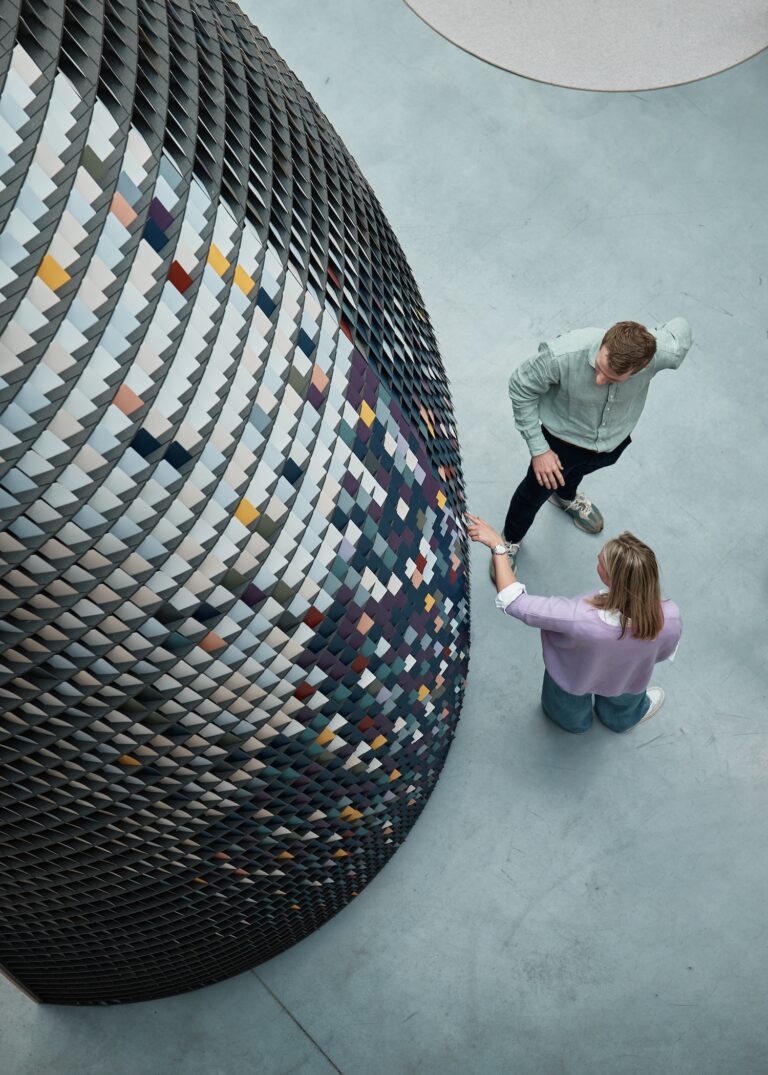
Computational design & optimization
The sculpture’s entire shape was determined by strategic CNC cutting calculations, prepared by our computational design expert. This approach ensured that the material is used as efficiently as possible, reducing off-cuts and scraps.
Local sourcing and manufacturing was also foreseen from the beginning. Every step of the manufacturing process took place within a 120-kilometer radius in Belgium. From panel creation in Izegem to woodworking in Wavre, Wallonia, this localized approach minimized transportation emissions, ensuring that the project is 100% made in Belgium. Additionally, the manufacturing process was designed to be simple and energy-efficient, relying on basic assembly techniques: puzzle-like assembly, bolts, screws, and minimal use of glue, optimizing energy consumption.
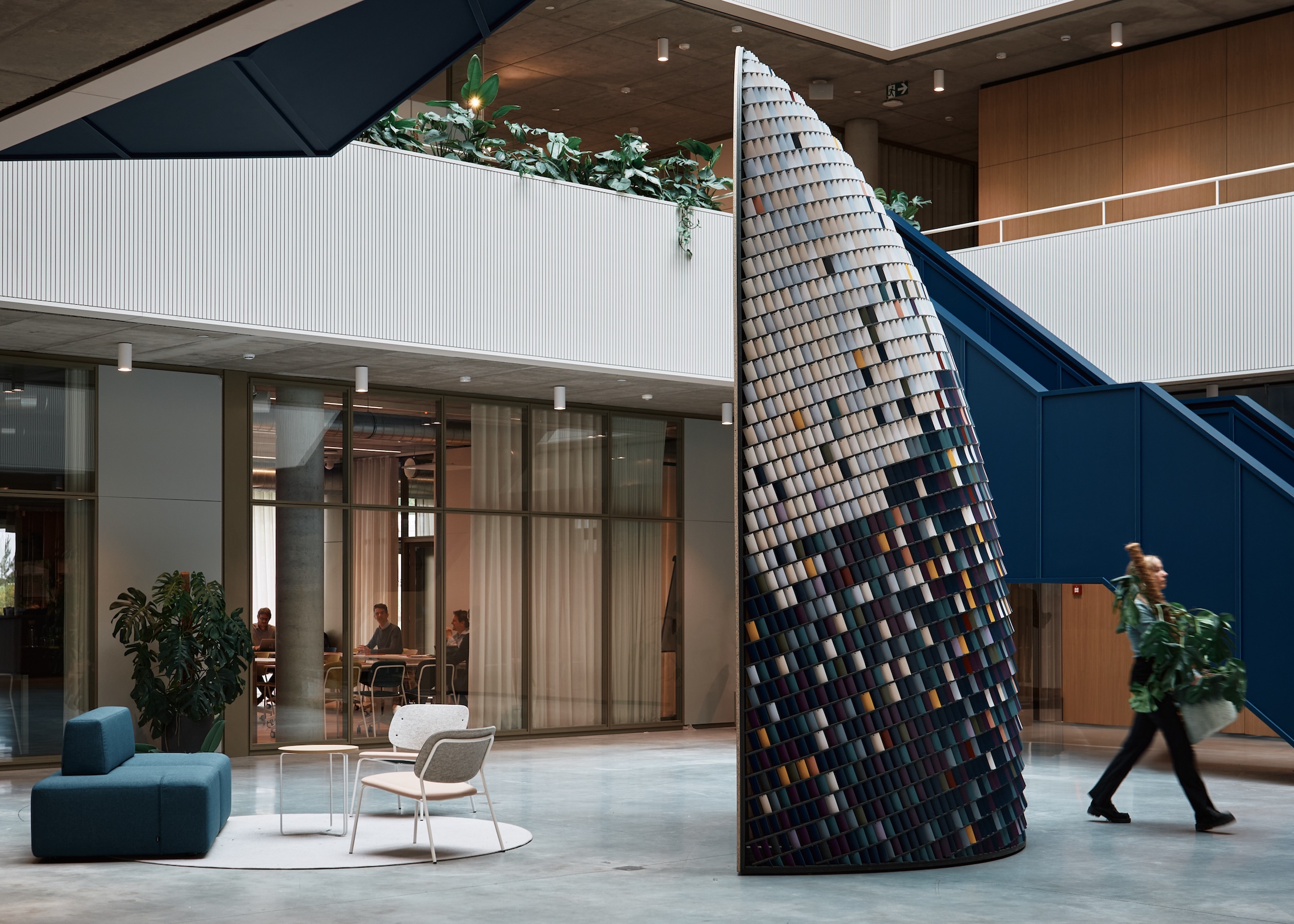
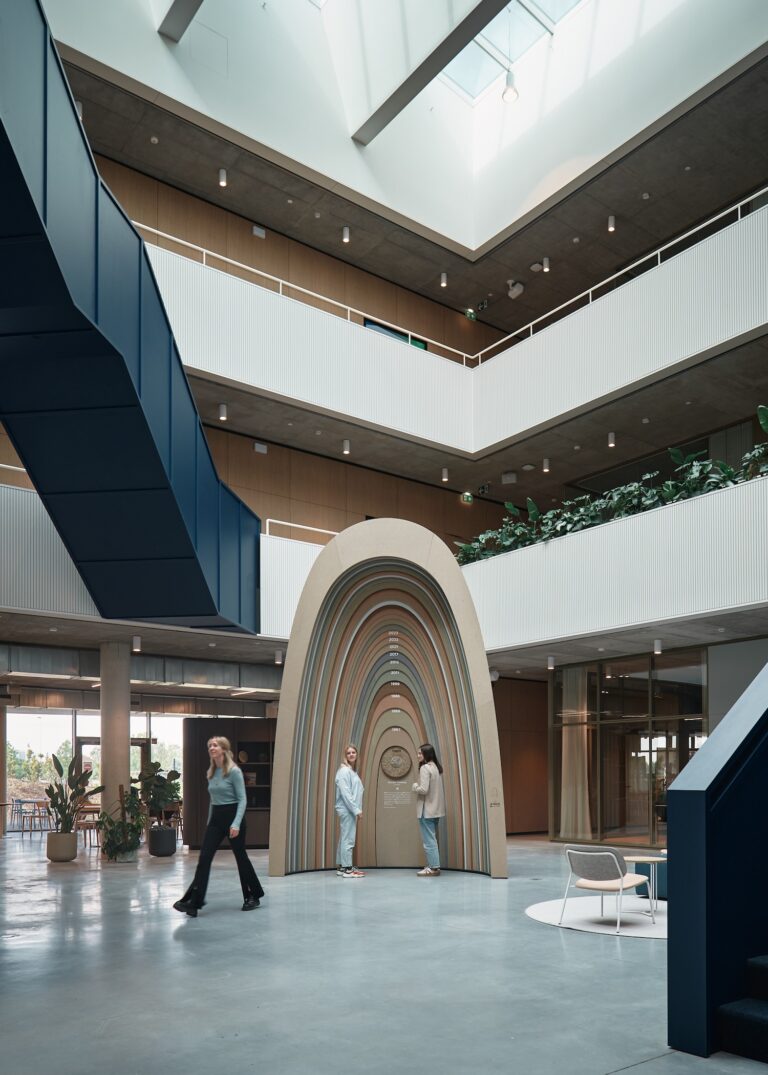
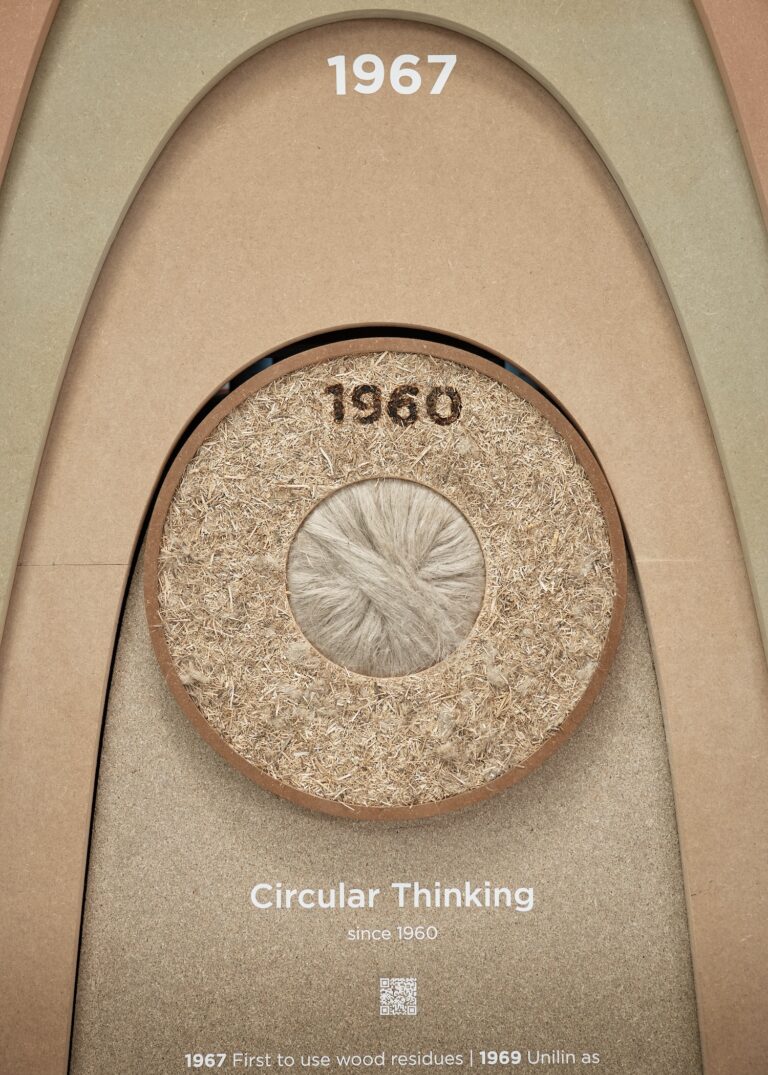
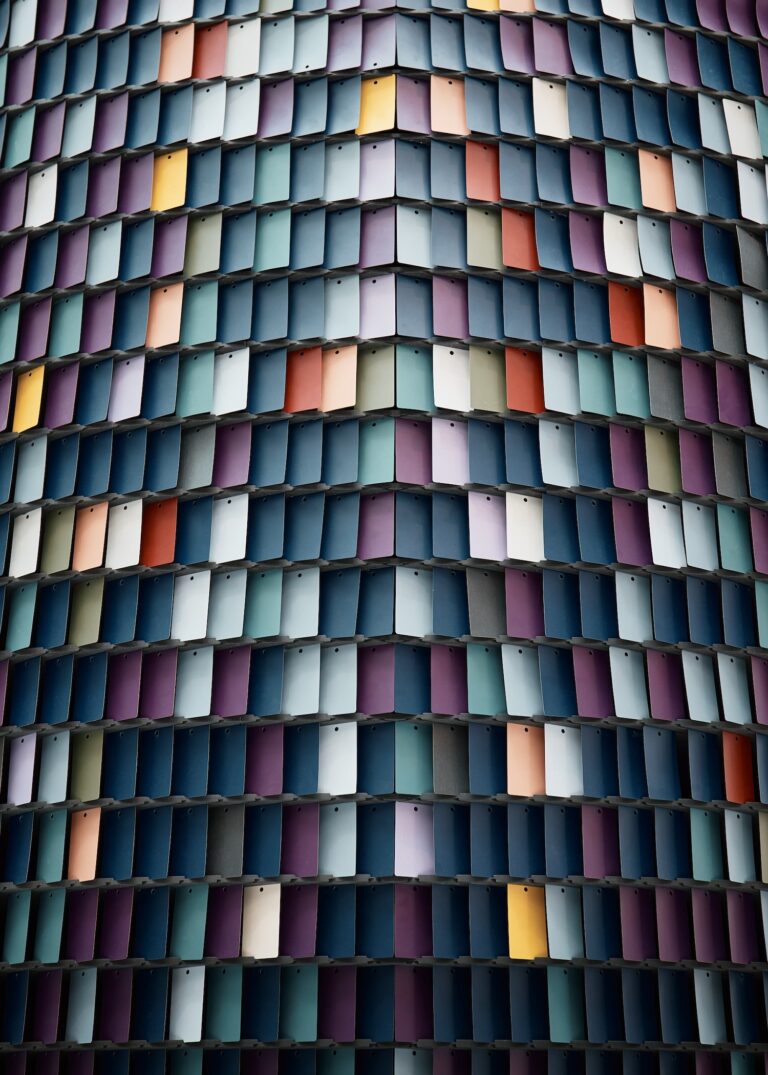
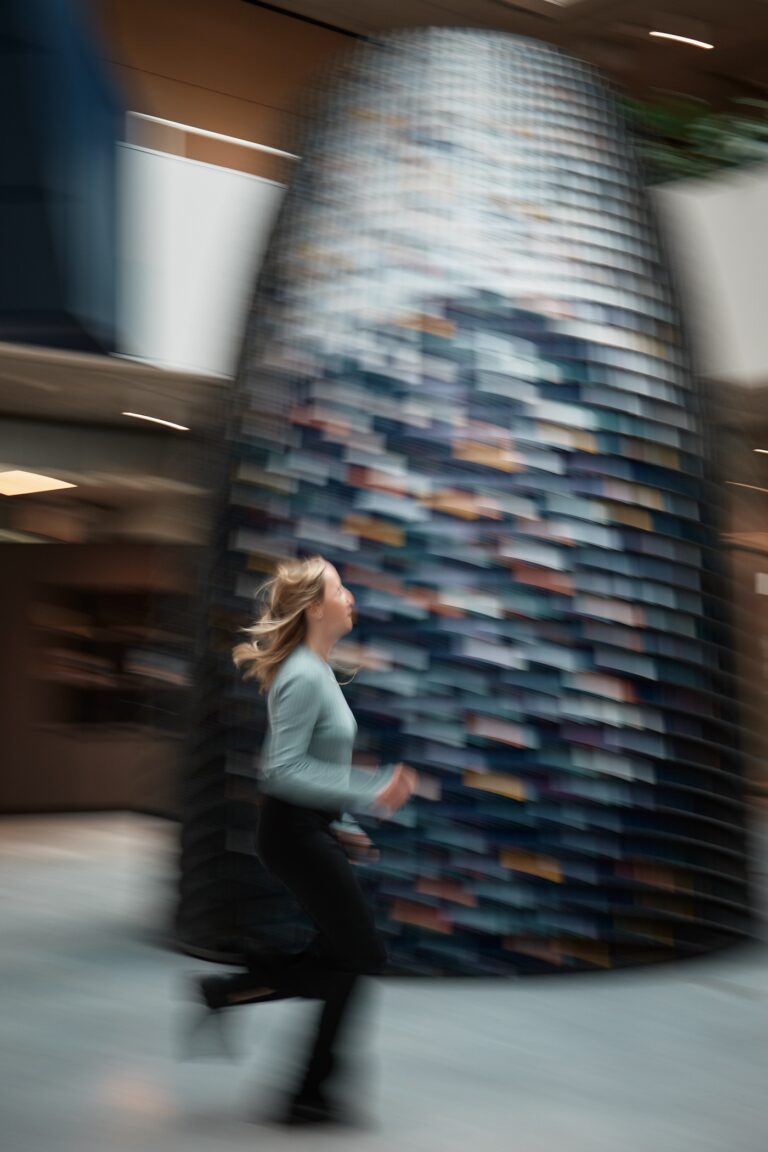
Project team
Alicia Finet
Mauro Brigham
Marc Martinez
Partners
Pictures by Atelier minHuy
Pluo